【2】 基板準備と位置合わせ
メタルマスクを使用してパターンを正確に転写するには、基板の事前準備と位置合わせの精度が極めて重要です。
①基板の準備
まずは、基板表面の洗浄と清浄化を行います。ほこりや微粒子、油分などの異物が付着していると、堆積材料が均一に乗らず、パターンの欠陥や密着不良につながる可能性があります。特にMEMS製品やセンサーのような高精度用途では、微小なゴミや汚れもパターン不良の原因となるため、細心の注意が払われます。
準備作業(1):超音波洗浄や薬液洗浄による表面の脱脂・粒子除去
準備作業(2):必要に応じて、乾燥・プラズマ処理
前提条件:微粒子や静電気を防ぐためのクリーンルーム内での作業
②位置合わせ(アライメント)
次に、メタルマスクと基板を正確に位置合わせする工程です。これは、マスクのパターンを基板上の正確な位置に一致させるための操作です。
注意事項(1):専用のアライメント装置を使用し、マスクと基板の相対位置を微調整
注意事項(2):顕微鏡やカメラでマークを確認しながらX・Y・θ(回転)のずれを補正
微細加工の場合、誤差は数ミクロン以下に抑える必要があります。高精度の堆積や蒸着を行う工程では、わずかなズレでも回路やパターンの欠陥につながるため、位置合わせの再現性と安定性が品質に直結します。
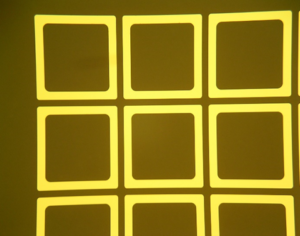
※ズレを防ぐための工夫は?
パターンの精度を保つためには、マスクと基板の相対位置の安定性が鍵になります。
①アライメントマークの設置
マスク・基板の両方に「目印(マーク)」を配置し、それをカメラで認識して自動補正。
②熱膨張の考慮
加熱処理を伴うプロセスでは、材料の膨張率の違いによるズレが起きやすいため、同一材料(例:Ni-Ni)を使ったり、室温で位置合わせする工夫も。
③フレーム設計
マスクの外周をしっかりと枠で支えることで、繰り返し使用時のズレや歪みを低減。
微細加工・パターン加工の詳細ページはこちら。
クシ形電極の標準在庫品はこちら。
【3】蒸着またはスパッタリングによるパターン成膜
メタルマスクの代表的な使用方法は、蒸着やスパッタリング、いわゆるPVD法での成膜によって、マスクのパターンを基板に転写する工程です。これはフォトリソグラフィとは異なり、光を使わず、材料そのものをマスクの開口部から堆積させる方法であり、シンプルかつ高精度な加工が可能です。
①真空蒸着
蒸着は、真空中で金属や有機材料を加熱・蒸発させ、その蒸気を基板へと飛ばして膜を形成する方法です。真空蒸着とは?はこちらから
◆仕組み
加熱源(抵抗加熱、電子ビームなど)で材料を蒸発 → 蒸気が直進し、メタルマスクの開口部を通過 → 基板上に選択的に堆積
◆特徴
・開口形状がそのまま反映されやすく、微細な形状も再現しやすい
・真空中で行うため、酸化や異物混入が少ない
◆主な用途
・センサー、MEMSの金属電極形成
・ミクロン領域の精密試作
②スパッタリング(Sputtering)
スパッタリングは、真空中に導入したアルゴンガスに高電圧を印加してプラズマ化し、そのイオンでターゲット材料を叩くことで、材料の粒子を基板に飛ばす手法です。スパッタリングとは?はこちらから
◆仕組み
Arイオンがターゲットに衝突 → 材料原子がはじき出される → メタルマスクの開口を通って基板に到達
◆特徴
・均一な膜厚を広範囲に形成可能
・高密着性の薄膜を得やすい
・蒸着に比べて指向性が弱く、マスクの影の影響を受けやすい
・複雑な材料(合金、酸化物など)も堆積しやすい。但し、ターゲットが必要。
◆主な用途
・電極パターンや導電配線の形成
・保護膜や機能性薄膜の堆積
・耐久性や導電性が求められる構造のパターン形成
※転写のポイントと課題
・蒸着は直進性が高く、微細パターン向き
・スパッタリングは密着性と耐久性に優れるが、パターンエッジのにじみ対策が必要
いずれも、マスクと基板の密着精度、固定方法、加工角度などが膜質やパターン精度に大きく影響します。
【4】マスクの取り外しから検査へ
メタルマスクを用いたパターン加工では、堆積工程が終わった後も、製品の品質を左右する重要な工程が続きます。それが「マスクの取り外し」と「検査」です。
①マスクの取り外し
材料の堆積が完了した後、メタルマスクを基板から慎重に取り外します。
◆注意点
・マスクと基板の密着を保ちながらも、ダメージを与えずに剥がす。
・高精度のパターンほど、取り外し時の微小なズレや歪みが歩留まりに影響。
・マスクが繰り返し使用される場合は、破損や汚染のチェックも重要。
・メカニカルチャックや真空吸着を用いた固定方式によっては、取り外し専用のツールや工程が必要になることもあります。
②検査
マスクを取り外したあとは、形成されたパターンの表面品質や寸法精度を確認します。必要に応じて、微細なゴミの除去や軽微な補正処理を行います。
◆主な確認項目と使用機器
・膜厚の均一性(膜厚計など)
・パターンの寸法精度と欠陥確認(光学顕微鏡、SEM)
・導通チェックや電気特性測定(電気プローブ)
また、量産工程では自動検査装置(AOI:自動光学検査装置)によって、数ミクロン単位の不良検出を行うこともあります。検査工程を経ることにより、当然ながら、「加工精度と再現性の確認」、「良品・不良品の判定」「次工程への品質保証」を確立させます。パターン加工の最終段階として、製品の信頼性と歩留まりを確保するための欠かせない工程です。
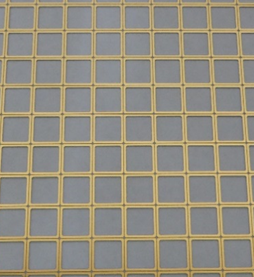
これらのプロセスを通じて、精密で高品質なパターン形成が実現します。メタルマスクは物理的な方法で直接パターンを転写するため、フォトリソグラフィーに比べて工程が少なく、迅速な加工が可能です。そのため、特にセンサーや高精度な導電パターンの形成に適した方法といえます。
繰り返しになりますが、使用環境や精度要求に応じた最適なマスクを選ぶことで、製品の品質・生産効率・コストが大きく左右されます。安達新産業では、こうしたニーズに応じて設計支援から製造・品質管理まで一貫対応し、お客様のものづくりを確かな技術で支えます。メタルマスクについて疑問、質問があれば、お気軽にお問い合わせください。
メタルマスクの基礎はこちらから